When it comes to building original Mustangs, Revology Cars is anything but conventional.
The norm in the low volume, specialty car business is to buy complete body shells from a supplier. But Orlando, Florida-based Revology builds its own shells – known as unibodies – by welding together individual parts.
Producing a unibody in this manner is how it’s done by major automakers. But for a small company, welding a unibody car structure from parts is a complex and challenging operation.
Despite this challenge, Revology embarked on the development of its own unibody production process more than two years ago and recently passed the 100th unibody milestone.
Why go to all this trouble? Revology production engineer, Kevin Capen, explains why the process is so important to the company and most importantly, the satisfaction of its customers.
“The main reasons are to improve body dimensional control, to ensure weld integrity, and to improve corrosion resistance.” says Capen. “Accurate dimensional control helps to solve issues in downstream assembly. We had been spending a lot of time fixing bodies that were being delivered to us. This is particularly important in terms of centering the frame rails on the cars and ensuring clearances for powertrain installation.”
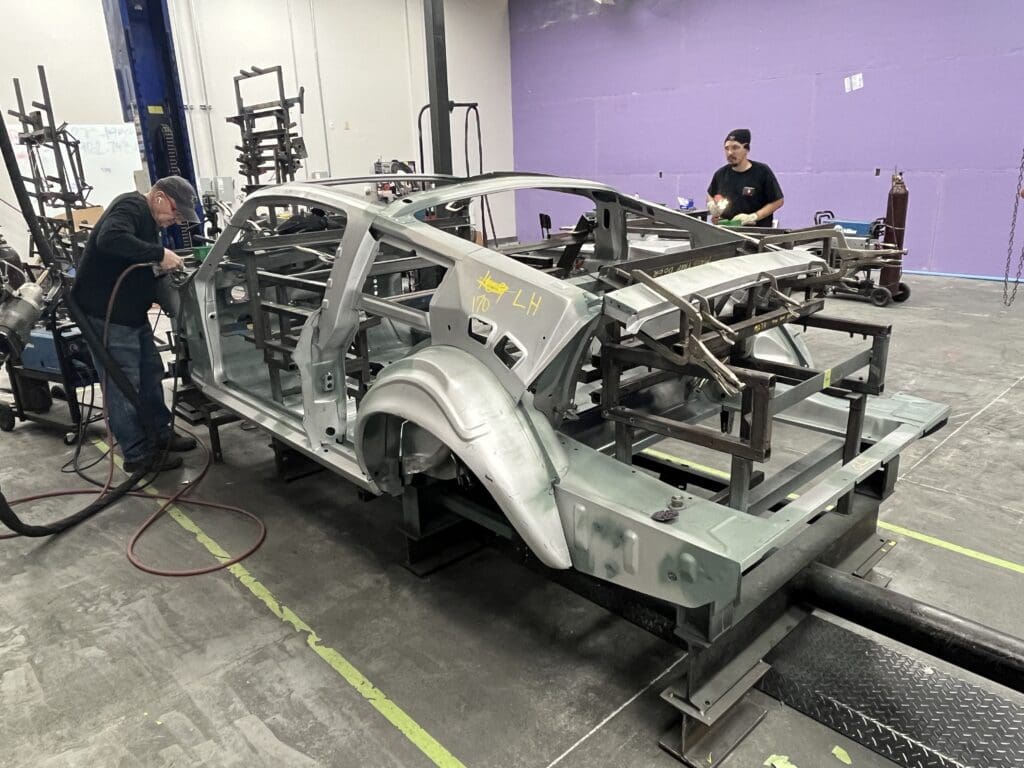
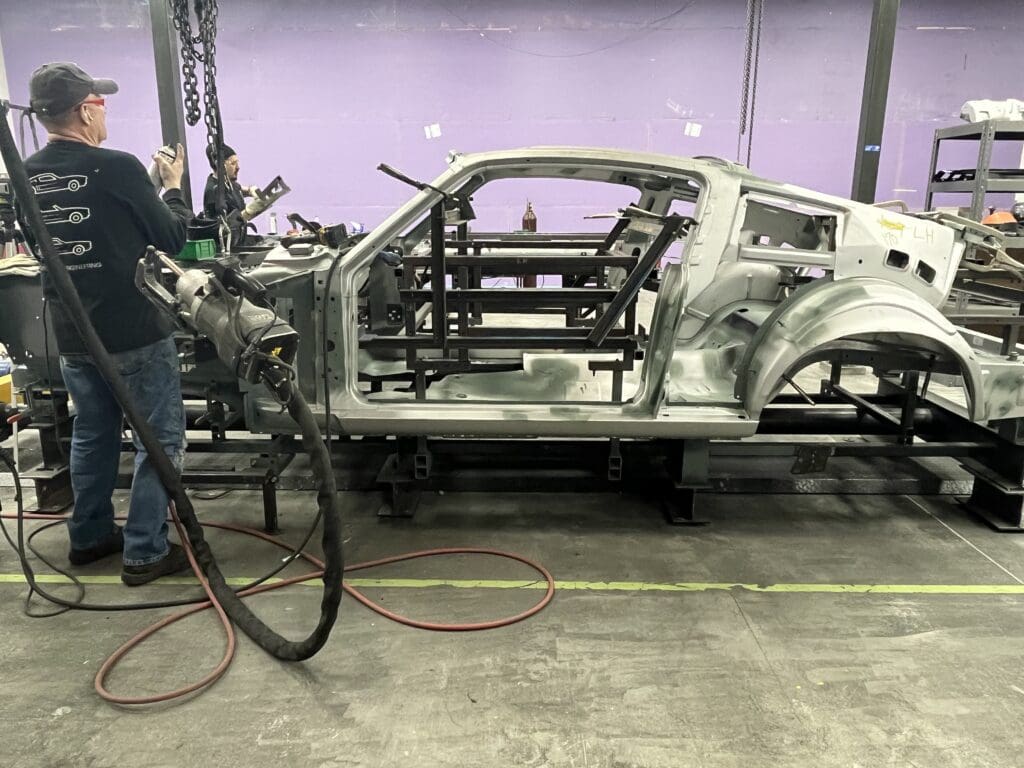
Capen says the quality of body welds has also been significantly improved. “We use automated “smart” spot welders that can adjust the weld schedule for each weld based on the material composition and thickness for that weld. Someone using a traditional spot welder would have to adjust weld schedules continuously, or settle on a compromised schedule, which can lead to cold welds.” Not to be confused with cold welding, which is a process that does not require heat or fusion to join two metals together, a cold weld is a weld that has inadequate penetration and therefore fails. At best, a cold weld can result in an annoying squeak or creak from the body when traveling over an undulating surface. At worst, it can result in a structural failure.
Corrosion resistance is improved because Revology can ensure every surface is prepared properly BEFORE it is assembled. The surface preparation process is time-consuming and the result of poor preparation may not be apparent until many years later, which may be an incentive for some builders to cut corners. However, Revology doesn’t cut corners. The company provides a five-year rust and corrosion warranty, identical to that offered by Ford on its current lineup, on every car it builds.
At Revology, the unibody production process involved the in-house development of custom fixtures to hold parts in place for welding. “We started the process with the 65-66 convertible Mustang, then added the ’65-66 fastback and then the ’67-68 fastback, so now we have all our body styles in unibody production,” says Capen. “Over time we have learned a lot in refining the process; what’s efficient, what’s critical and so on.”
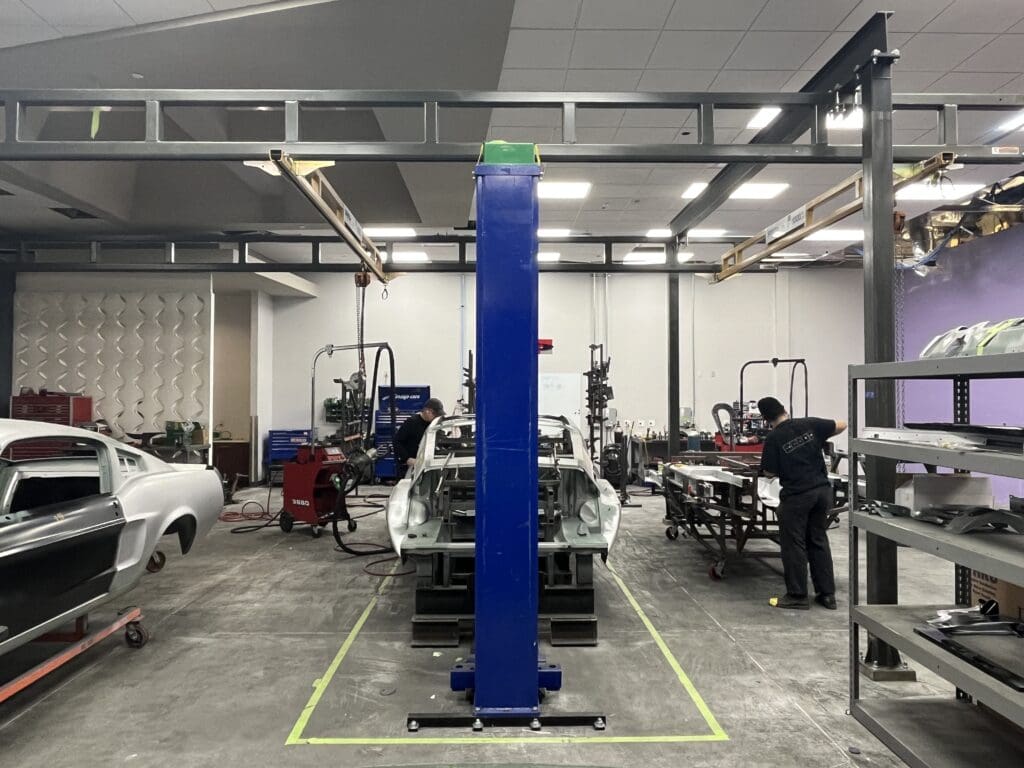
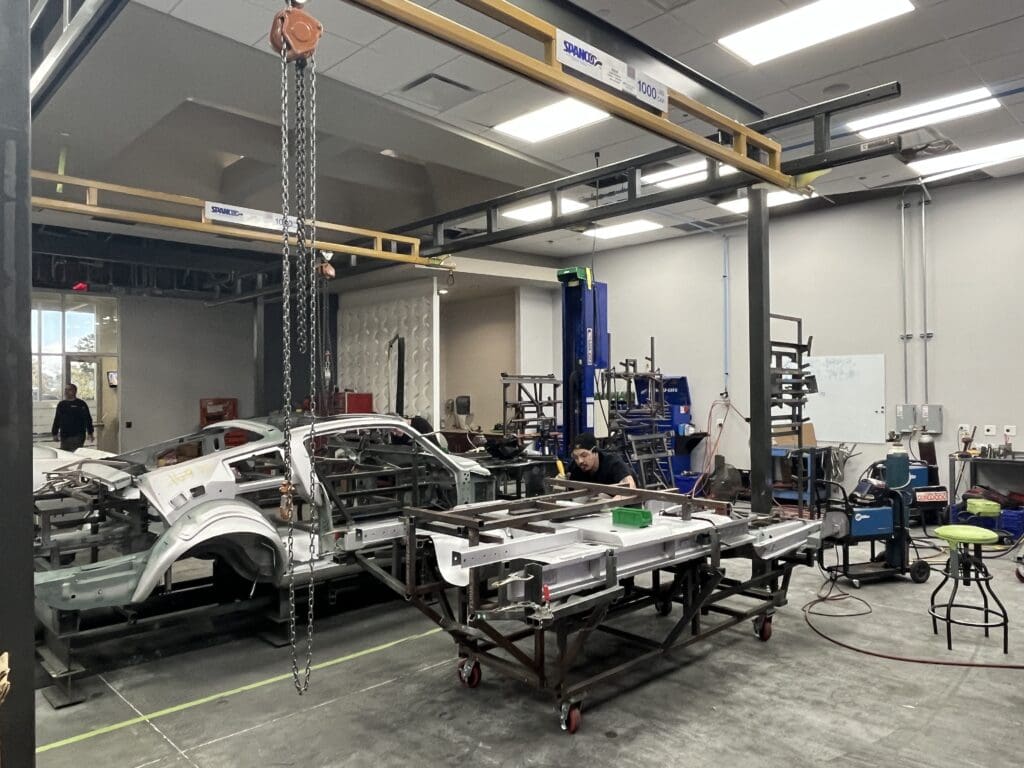
What all this means for the Revology customer is a higher quality body, one that is dimensionally accurate, more rigid, has consistent panel fits and improved corrosion protection. It also means that production time is being reduced. Says Capen, We’re working towards a faster built vehicle with a lot more quality and efficiency. So, customer delivery times will come down and quality will continuously improve.”
“When we launched Revology Cars, we thought we could outsource certain aspects of the manufacturing process,” says Tom Scarpello, Revology Cars’ Founder and CEO. “However, our experience has been just the opposite—to ensure the level of quality our customers demand, at the target price, and be able to deliver on time, we have had to vertically integrate. Today, we not only build the body, we do all paint and assembly work in-house as well. It is the only way to control the process.”