What does it take to build a car as finely crafted as a Revology Mustang?
Put simply, it comes down to applying big automaker processes on a micro-scale.
Knowledge, skills, experience are all critical, but the key to Revology Cars’ success is employment of the same sophisticated manufacturing processes used by the world’s top car companies.
Even though the Florida-based reproduction original Mustang builder produces only six cars a month right now, Revology’s management team has its sights on growth. And they know that to grow they must have robust process controls, just like an OEM that builds hundreds or thousands of vehicles daily.
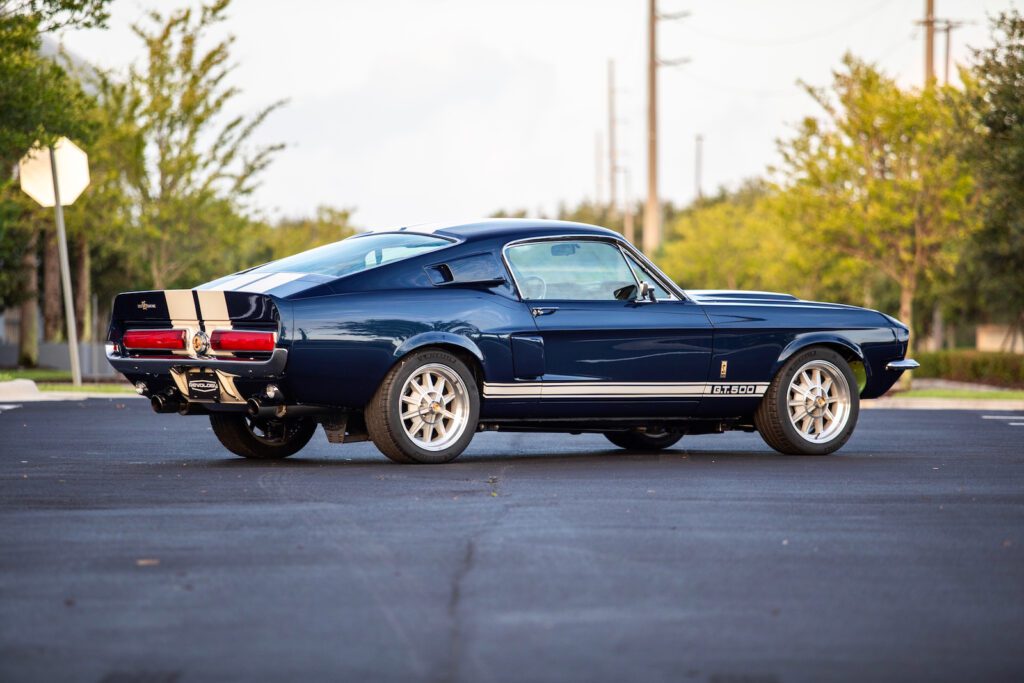
It’s an approach Revology Cars CEO and founder Tom Scarpello says clearly separates the company from other small volume, specialty car producers.
“There is a huge gap in manufacturing process capability between the OEMs and the aftermarket industry,” says Scarpello. “Typically, aftermarket companies rely heavily on the skills of a handful of highly experienced individuals, often including the owner of the company, to ensure product quality. However, they have difficulty scaling because they don’t have robust manufacturing processes. When that expert is no longer able to personally oversee everything, quality suffers.”
The Revology manufacturing process is a far cry from the reality show hot rod shop environment that many people associate with the specialty automotive segment. In stark contrast to their entertainment industry counterparts, Revology employees and managers concern themselves with dry-sounding tasks, such as cycle times, resource planning, mix and model line balancing, tooling, equipment, and fixture development, advanced product quality planning (APQP), production part approval process (PPAP), failure mode and effects analysis (FMEA), measurement systems analysis (MSA), statistical process control (SPC), and a host of other manufacturing tools and metrics.
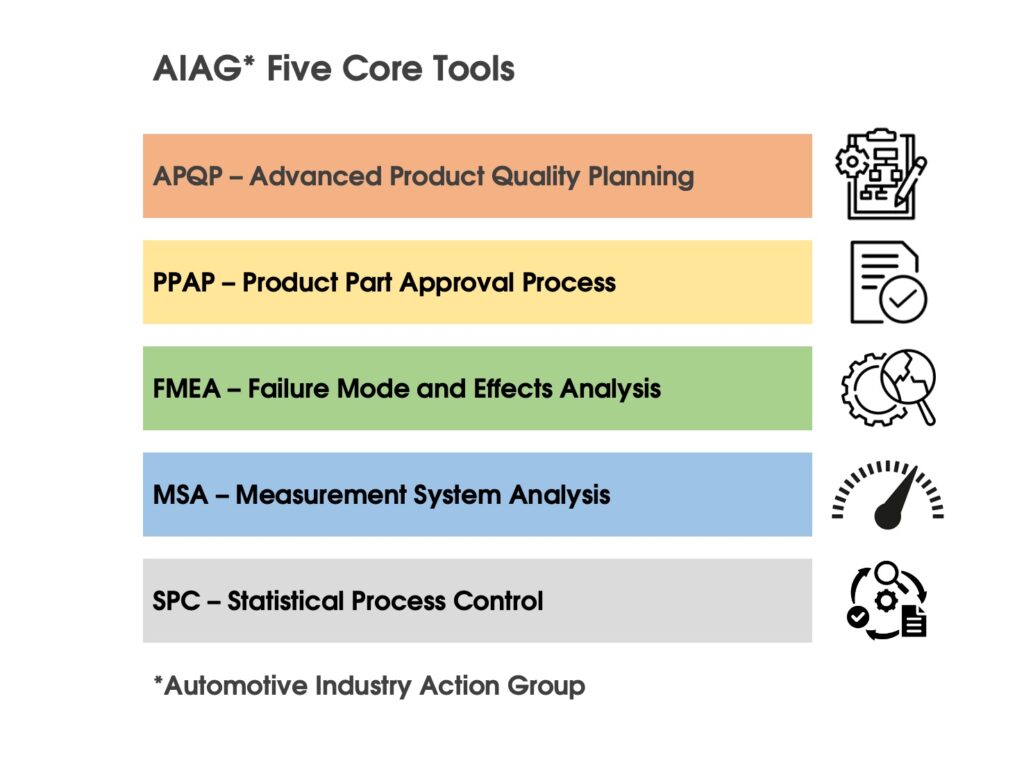
“The mindset of the custom car builder is that every car he builds is unique—but the mindset in manufacturing is that every car we build is the same. It is a fundamental difference,” says Scarpello. “It is a lot of work, which is why nobody else producing vehicles in small volumes does it.”
All of this may sound daunting, but it’s familiar to anyone with experience in the high production volume auto industry. And that’s another key enabler at Revology: many of the company’s managers have cut their teeth at major OEMs, such as Ford and Honda. In fact, Scarpello started his career on the floor of a Ford manufacturing plant, as a supervisor in the Body department of Ford’s Wayne Assembly plant, in Wayne, Michigan.
Another key Revology player is Aaron Wright, chief engineer for product development. Wright hails from Honda research and development operations in Ohio and understands deeply how one of the world’s most proficient manufacturers employs robust process capability to ensure product quality.
“Ford, Honda, and other OEMs are all about process, and we try to emulate them as much as we can,” says Wright. Even though they are much larger companies, we operate using many of the same fundamental principles.”
Revology customers love their cars for their performance and personality, but they may not realize just how much painstaking work and planning goes into their production.
What all this management experience and knowledge means is that Revology can function with the efficiency, quality control and repeatability of a large automaker, even while making a fraction of the number of cars.
“We operate like Ford on a micro-scale,” notes Revology marketing and sales director Yoshi Amano. “It’s what puts us on a different level from the rest of the specialty industry.”