Sophisticated assembly technologies are normally confined to large automakers, but Revology Cars is once again upping its game by adopting a high-tech process.
Going forward, all Revology models will use structural adhesives in conjunction with spot welding to create stronger stiffer bodies, a move which brings a host of customer pleasing improvements.
Company CEO Tom Scarpello explains that structural adhesives developed in the aerospace industry and were introduced into automotive manufacturing in the 1980s and 1990s. BMW and Audi were among early adopters of the concept but with technical advances and lowered costs, structural adhesives went mainstream by 2010.
One prominent example was the aluminum-bodied 2015 Ford F-150 truck, which relied heavily on structural adhesives.
“There are many benefits to using structural adhesives at the body-in-white (pre-painting) assembly stage of production,” says Scarpello.
Tests performed by Honda indicated that the application of structural adhesives can improve the rigidity of a body by 40 to 60 percent.
“This is a massive increase in torsional rigidity which results in a much stiffer body,” notes Scarpello. This means no squeaks, rattles, or vibration. It also allows us to optimize the suspension tuning.”
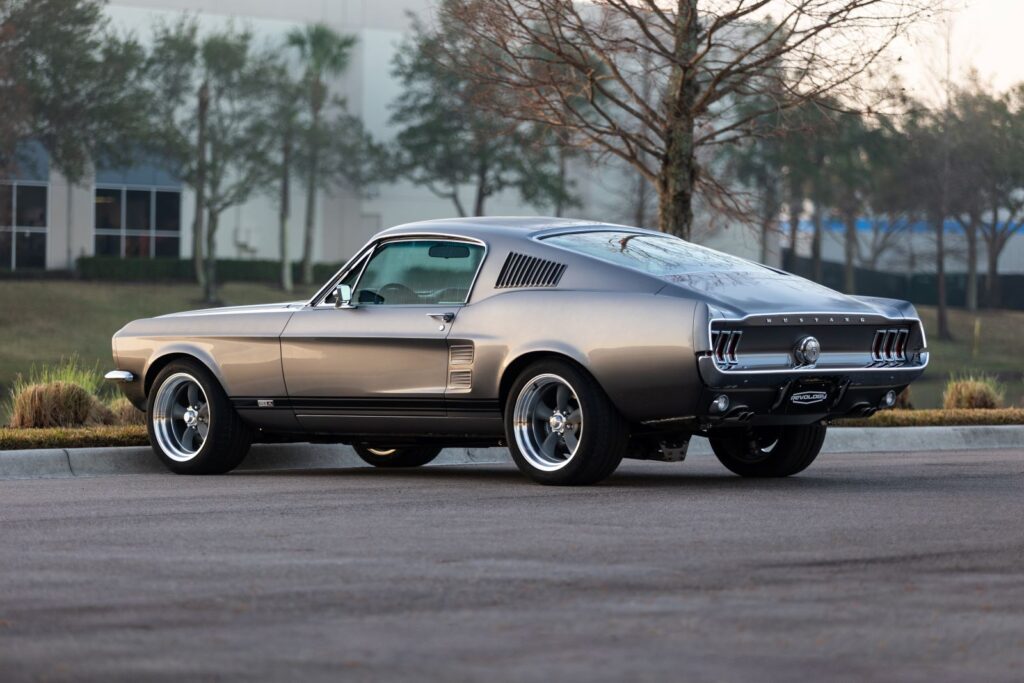
Another benefit is improved corrosion resistance. The structural adhesive covers the entire flange so it is completely sealed. “In addition to spot welds the flange is now fully sealed, which means there is nowhere for corrosion to take hold,” says Scarpello.
A further advantage is improved durability, as structural adhesive reduces vibrations and thus improves long term structural integrity of the body.
Finally, the adhesive helps improve crash safety by evenly distributing impact forces throughout the body.
Why is this development a big deal for Revology, which is already the leader in the specialty segment for assembly processes?
“The fact no-one else in the segment is doing it tells you something,” Scarpello points out. “It’s difficult, it requires specialized expertise, a major investment and it increases assembly time.
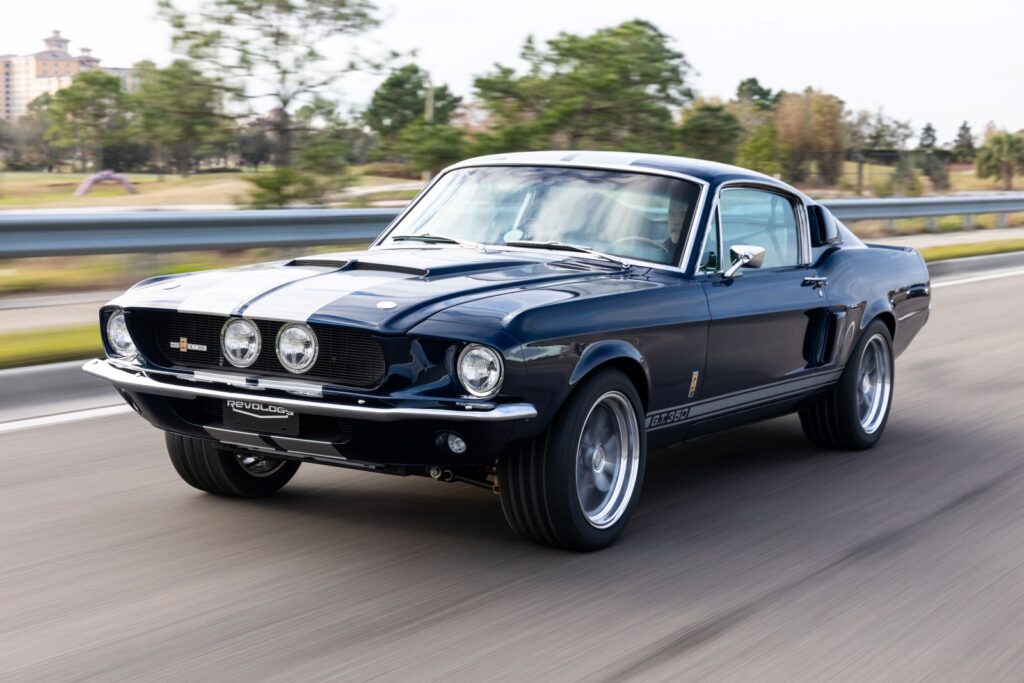
“We already have the best built body-in-white in the industry, but the application of structural adhesive on top of that very well built body provides an incremental benefit.
“It’s the right thing to do,” adds Scarpello. “It’s our mission to continually push for improvements, to continually find ways to make the best possible product. Bean counters will ask you why are you doing that, why are you spending the money to do it, you are already the best in the segment? It’s because we know our customer and our customer wants the best.”